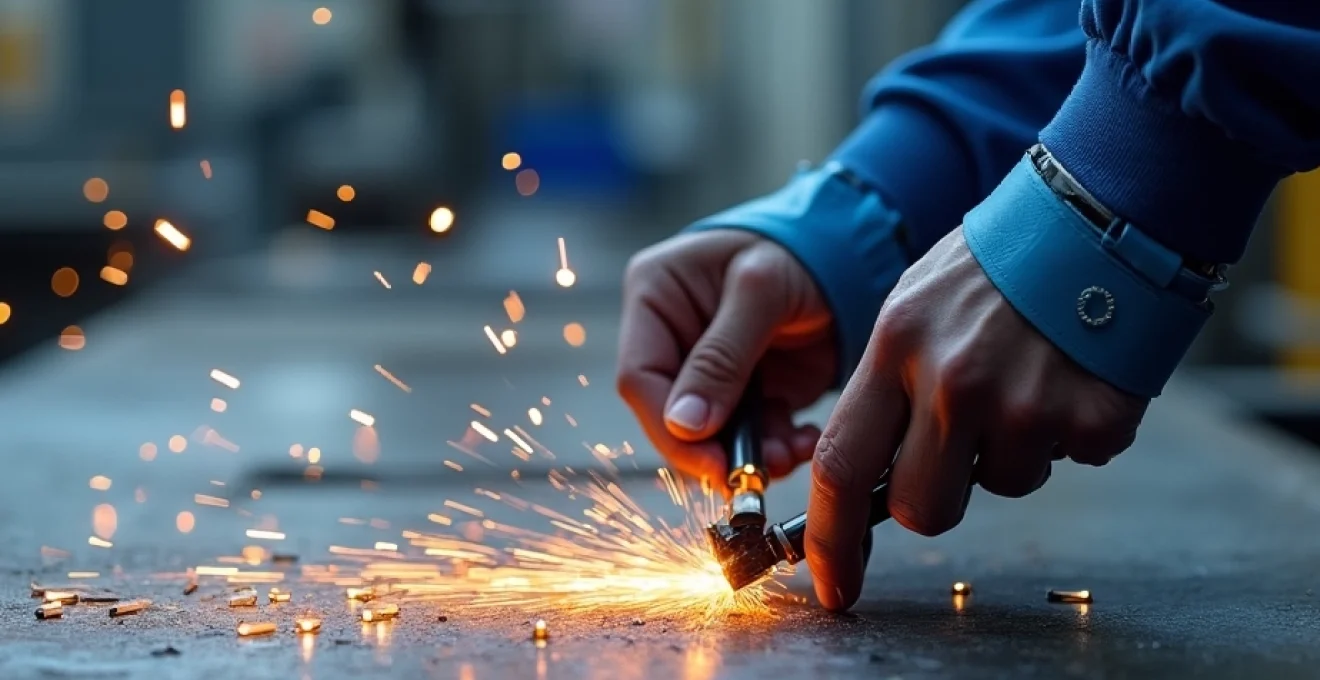
Le traitement de surface des métaux joue un rôle crucial dans l'amélioration de leurs propriétés et de leur durabilité. Cette étape essentielle permet de modifier les caractéristiques superficielles des matériaux métalliques, leur conférant une meilleure résistance à la corrosion, à l'usure et aux agressions chimiques. En optimisant les performances des métaux, ces traitements ouvrent la voie à de nouvelles applications dans divers secteurs industriels, de l'automobile à l'aérospatiale en passant par l'électronique.
L'importance du traitement de surface ne saurait être sous-estimée. Il permet non seulement de prolonger la durée de vie des pièces métalliques, mais aussi d'améliorer leur aspect esthétique et leurs propriétés fonctionnelles. Dans un monde où l'efficacité et la durabilité sont primordiales, maîtriser les techniques de traitement de surface est devenu un enjeu majeur pour les industriels et les ingénieurs des matériaux.
Techniques de traitement de surface des métaux
Il existe une grande variété de techniques de traitement de surface des métaux, chacune adaptée à des besoins spécifiques et offrant des avantages particuliers. Ces méthodes peuvent être classées en plusieurs catégories, notamment les traitements mécaniques, chimiques, électrochimiques et thermiques. Le choix de la technique appropriée dépend de nombreux facteurs, tels que la nature du métal, l'environnement d'utilisation et les propriétés recherchées.
Parmi les techniques les plus couramment utilisées, on trouve le revêtement par projection thermique, la galvanisation à chaud et l'anodisation de l'aluminium. Ces procédés ont révolutionné le traitement de surface des métaux, offrant des solutions performantes pour améliorer la résistance et la durabilité des matériaux métalliques dans diverses applications industrielles.
Revêtement par projection thermique
Le revêtement par projection thermique est une technique avancée qui consiste à projeter des particules de matériau fondu ou semi-fondu sur une surface métallique. Ce procédé permet de créer des couches protectrices épaisses et adhérentes, offrant une excellente résistance à l'usure et à la corrosion. La projection thermique est particulièrement efficace pour les pièces de grandes dimensions ou de formes complexes.
Cette méthode présente plusieurs avantages :
- Une grande flexibilité dans le choix des matériaux de revêtement
- Une application rapide et précise
- La possibilité de traiter des pièces de grandes dimensions
- Une excellente adhérence du revêtement au substrat
La projection thermique est largement utilisée dans l'industrie aérospatiale, automobile et énergétique, où elle permet de protéger efficacement les composants soumis à des conditions extrêmes. Par exemple, les turbines à gaz bénéficient grandement de cette technique pour résister aux hautes températures et à l'érosion.
Galvanisation à chaud
La galvanisation à chaud est un procédé de traitement de surface largement répandu, particulièrement efficace pour protéger l'acier contre la corrosion. Cette technique consiste à immerger les pièces métalliques dans un bain de zinc fondu, créant ainsi une couche protectrice qui agit comme une barrière contre les agents corrosifs. La galvanisation à chaud offre une protection durable et économique, faisant d'elle une solution privilégiée dans de nombreux secteurs industriels.
Les avantages de la galvanisation à chaud sont nombreux :
- Une protection anticorrosion de longue durée
- Une résistance mécanique accrue
- Un coût relativement faible par rapport à d'autres traitements
- Une application possible sur des pièces de grandes dimensions
Cette technique est couramment utilisée dans la construction, les infrastructures routières et les équipements urbains. Par exemple, les garde-corps, les pylônes électriques et les structures métalliques extérieures bénéficient souvent de ce traitement pour résister aux intempéries et à la corrosion atmosphérique.
Anodisation de l'aluminium
L'anodisation est un procédé électrochimique spécifiquement développé pour le traitement de surface de l'aluminium et de ses alliages. Cette technique consiste à créer une couche d'oxyde protectrice à la surface du métal, améliorant ainsi sa résistance à la corrosion et à l'usure. L'anodisation offre également la possibilité de colorer la surface, ce qui en fait une solution prisée dans les applications esthétiques.
Les principaux avantages de l'anodisation sont :
- Une excellente résistance à la corrosion
- Une dureté de surface accrue
- La possibilité de coloration dans une large gamme de teintes
- Une bonne isolation électrique
L'anodisation est largement utilisée dans l'industrie aérospatiale, l'architecture et l'électronique grand public. Par exemple, les boîtiers d'ordinateurs portables et de smartphones sont souvent anodisés pour améliorer leur durabilité et leur esthétique. Selon les experts de hnk-electroplating.com, l'anodisation permet d'obtenir des finitions de haute qualité tout en préservant les propriétés mécaniques de l'aluminium.
Préparation des surfaces avant le traitement
La préparation des surfaces est une étape cruciale dans le processus de traitement de surface des métaux. Une surface mal préparée peut compromettre l'efficacité du traitement et réduire considérablement sa durée de vie. Cette phase préliminaire vise à éliminer toutes les impuretés, les contaminants et les défauts de surface qui pourraient nuire à l'adhérence et à la qualité du revêtement.
La préparation des surfaces comprend généralement plusieurs étapes :
- Nettoyage : élimination des graisses, huiles et autres contaminants
- Décapage : suppression des oxydes et de la rouille
- Sablage ou grenaillage : création d'une rugosité de surface optimale
- Rinçage : élimination des résidus de traitement
- Séchage : évacuation de l'humidité résiduelle
Le choix de la méthode de préparation dépend de plusieurs facteurs, notamment la nature du métal, le type de contaminants présents et le traitement de surface envisagé. Par exemple, le sablage est particulièrement efficace pour créer une rugosité de surface optimale avant l'application d'un revêtement par projection thermique, tandis que le décapage chimique est souvent privilégié pour la préparation des pièces destinées à la galvanisation.
Il est important de noter que la qualité de la préparation de surface a un impact direct sur les performances du traitement de surface. Une surface mal préparée peut entraîner des problèmes tels que le décollement du revêtement, une adhérence insuffisante ou une protection inadéquate contre la corrosion. Investir dans une préparation de surface rigoureuse est donc essentiel pour garantir la durabilité et l'efficacité du traitement.
Choix du traitement selon l'application finale
Le choix du traitement de surface approprié est une décision cruciale qui dépend de nombreux facteurs, notamment l'application finale du produit, l'environnement d'utilisation et les propriétés recherchées. Chaque technique de traitement offre des avantages spécifiques et convient à certaines applications mieux que d'autres. Il est donc essentiel de bien comprendre les exigences du projet pour sélectionner le traitement le plus adapté.
Voici quelques exemples de critères à prendre en compte lors du choix d'un traitement de surface :
- Résistance à la corrosion requise
- Contraintes mécaniques subies par la pièce
- Conditions environnementales (température, humidité, agents chimiques)
- Aspect esthétique souhaité
- Coût et durée de vie attendue
Par exemple, pour des applications en milieu marin, où la résistance à la corrosion est primordiale, on privilégiera des traitements tels que la galvanisation à chaud ou l'application de revêtements spéciaux résistants à l'eau de mer. Dans l'industrie alimentaire, où l'hygiène est une priorité, on optera plutôt pour des traitements comme l' électropolissage de l'acier inoxydable, qui facilite le nettoyage et prévient l'adhérence des bactéries.
Le tableau suivant présente une comparaison de différents traitements de surface en fonction de leurs caractéristiques et applications principales :
Traitement | Résistance à la corrosion | Résistance à l'usure | Applications typiques |
---|---|---|---|
Galvanisation à chaud | Excellente | Moyenne | Construction, infrastructures |
Anodisation | Bonne | Bonne | Aérospatiale, électronique |
Nickelage chimique | Très bonne | Excellente | Automobile, industrie chimique |
Peinture poudre | Bonne | Moyenne | Mobilier urbain, électroménager |
Il est important de noter que dans certains cas, une combinaison de plusieurs traitements peut être nécessaire pour obtenir les propriétés souhaitées. Par exemple, un revêtement duplex associant une galvanisation à chaud suivie d'une peinture poudre peut offrir une protection anticorrosion exceptionnelle pour des applications en environnement très agressif.
Contrôle qualité des traitements de surface
Le contrôle qualité est une étape essentielle dans le processus de traitement de surface des métaux. Il permet de s'assurer que le traitement appliqué répond aux spécifications requises et offre les performances attendues. Un contrôle rigoureux est indispensable pour garantir la fiabilité et la durabilité des pièces traitées, en particulier dans les secteurs où la sécurité et la performance sont critiques.
Les méthodes de contrôle qualité varient en fonction du type de traitement et des propriétés à vérifier. Voici quelques techniques couramment utilisées :
- Mesure de l'épaisseur du revêtement
- Tests d'adhérence
- Essais de corrosion accélérée
- Contrôle visuel et dimensionnel
- Analyse de la composition chimique de surface
Par exemple, pour évaluer la qualité d'une galvanisation à chaud, on utilisera des techniques telles que la spectrométrie à fluorescence X pour mesurer l'épaisseur de la couche de zinc, et des tests de brouillard salin
pour évaluer la résistance à la corrosion. Pour l'anodisation, on effectuera des mesures d'épaisseur de couche d'oxyde et des tests de dureté de surface.
Il est important de noter que le contrôle qualité ne se limite pas à la vérification du produit fini. Il intervient à toutes les étapes du processus de traitement, de la préparation de surface à l'application du revêtement. Cette approche globale permet de détecter et de corriger rapidement les éventuels problèmes, assurant ainsi une qualité constante et optimale.
Impact environnemental des traitements de surface
L'impact environnemental des traitements de surface des métaux est une préoccupation croissante dans l'industrie. Certains procédés traditionnels utilisent des substances chimiques potentiellement dangereuses et génèrent des déchets toxiques. Face à ces enjeux, le secteur s'efforce de développer des solutions plus respectueuses de l'environnement, tout en maintenant les performances techniques requises.
Plusieurs approches sont mises en œuvre pour réduire l'empreinte écologique des traitements de surface :
- Utilisation de produits chimiques moins toxiques
- Optimisation des processus pour réduire la consommation d'eau et d'énergie
- Mise en place de systèmes de traitement et de recyclage des effluents
- Développement de technologies de traitement à sec
- Adoption de revêtements à base d'eau ou de poudre
Par exemple, dans le domaine de la galvanisation, des efforts sont réalisés pour remplacer le chrome hexavalent
, une substance cancérigène, par des alternatives moins toxiques comme le chrome trivalent . Dans l'industrie de la peinture, l'utilisation croissante de peintures à base d'eau et de poudre permet de réduire considérablement les émissions de composés organiques volatils (COV).
L'industrie du traitement de surface s'oriente également vers des procédés plus économes en énergie. Par exemple, l'utilisation de fours à induction pour la galvanisation à chaud permet de réduire la consommation énergétique tout en améliorant le contrôle de la température du bain de zinc. De même, les technologies de projection thermique à froid, qui ne nécessitent pas de chauffer le matériau de revêtement à des températures élevées, offrent une alternative plus écologique aux méthodes traditionnelles.
Il est important de noter que l'impact environnemental d'un traitement de surface ne se limite pas à sa phase d'application. La durabilité et la performance du traitement jouent également un rôle crucial. Un revêtement de haute qualité qui prolonge significativement la durée de vie d'un produit peut avoir un impact environnemental positif à long terme en réduisant la nécessité de remplacement et donc la consommation de ressources.