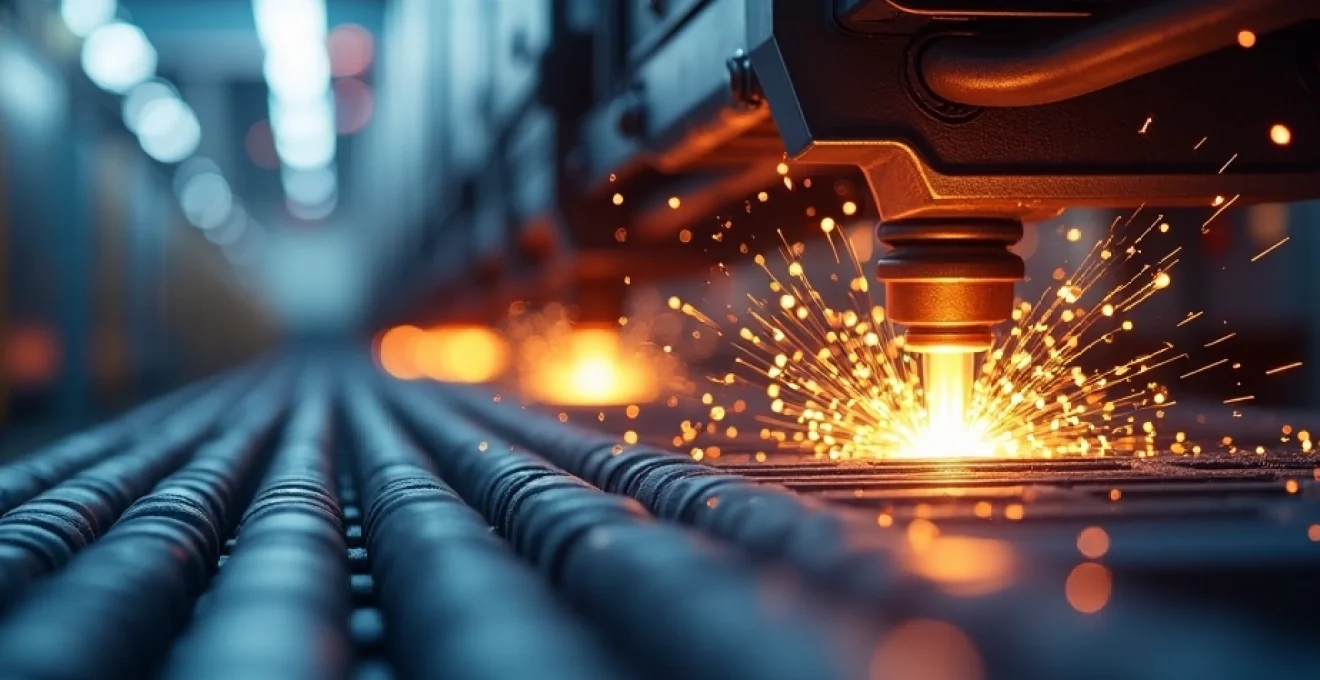
La chaudronnerie industrielle a connu une révolution silencieuse ces dernières années. Les avancées technologiques ont transformé ce secteur traditionnel en une industrie de pointe, capable de répondre aux exigences les plus strictes en matière de précision et d'efficacité. Aujourd'hui, les entreprises qui adoptent ces innovations peuvent optimiser leur production de manière significative, réduisant les coûts tout en améliorant la qualité de leurs produits. Comment ces nouvelles technologies peuvent-elles propulser votre entreprise vers de nouveaux sommets de productivité ?
Évolution technologique de la chaudronnerie industrielle
L'évolution de la chaudronnerie industrielle est marquée par l'intégration de technologies de pointe qui ont révolutionné les processus de fabrication. Les ateliers modernes, comme ceux de capelli.fr, sont désormais équipés de machines à commande numérique qui offrent une précision inégalée. Cette transformation digitale a permis d'automatiser de nombreuses tâches, réduisant ainsi les erreurs humaines et augmentant la productivité.
L'utilisation de capteurs avancés et de l'Internet des Objets (IoT) dans les équipements de chaudronnerie permet un suivi en temps réel des processus de fabrication. Ces technologies fournissent des données précieuses qui peuvent être analysées pour optimiser la production, prédire les maintenances nécessaires et réduire les temps d'arrêt. La révolution numérique a également touché la conception, avec des logiciels de modélisation 3D qui permettent de visualiser et de tester virtuellement les pièces avant leur fabrication.
L'intelligence artificielle commence à jouer un rôle crucial dans l'optimisation des processus de chaudronnerie. Les algorithmes d'apprentissage automatique peuvent analyser des milliers de paramètres pour déterminer les configurations optimales des machines, permettant ainsi d'améliorer constamment la qualité et l'efficacité de la production. Cette évolution technologique a non seulement augmenté la productivité, mais a également ouvert la voie à de nouvelles possibilités en termes de conception et de personnalisation des produits.
Procédés avancés de fabrication en chaudronnerie moderne
Les procédés de fabrication en chaudronnerie moderne ont connu des avancées significatives, permettant une précision et une efficacité sans précédent. Ces nouvelles techniques ont transformé la manière dont les pièces métalliques sont conçues, fabriquées et assemblées, offrant aux industriels des possibilités auparavant inimaginables.
Découpe laser de précision avec machines trumpf TruLaser
La découpe laser de précision, notamment avec les machines Trumpf TruLaser, représente une avancée majeure dans le domaine de la chaudronnerie. Ces équipements de pointe permettent une découpe ultra-précise des métaux, avec des tolérances extrêmement faibles, de l'ordre du dixième de millimètre. La technologie laser offre également l'avantage de réduire considérablement les déchets de matière première, optimisant ainsi l'utilisation des ressources.
Les machines TruLaser sont capables de découper une grande variété de matériaux, y compris les aciers inoxydables, l'aluminium et même des matériaux composites. Leur vitesse de découpe élevée, combinée à leur précision, permet d'augmenter significativement la productivité tout en maintenant une qualité constante. De plus, la flexibilité de ces systèmes permet de passer rapidement d'un type de pièce à un autre, réduisant ainsi les temps de configuration et augmentant la réactivité face aux demandes des clients.
Soudage robotisé et systèmes de vision artificielle
Le soudage robotisé, associé aux systèmes de vision artificielle, a révolutionné les processus d'assemblage en chaudronnerie. Les robots de soudage, équipés de caméras haute résolution et d'algorithmes de traitement d'image sophistiqués, peuvent réaliser des soudures complexes avec une précision et une régularité impossibles à atteindre manuellement. Cette technologie permet non seulement d'améliorer la qualité des soudures, mais aussi d'augmenter considérablement la vitesse de production.
Les systèmes de vision artificielle jouent un rôle crucial dans ce processus. Ils analysent en temps réel la géométrie des pièces à assembler, détectent les éventuelles déformations ou défauts, et ajustent automatiquement les paramètres de soudage pour garantir un résultat optimal. Cette capacité d'adaptation en temps réel permet de réduire les rebuts et d'assurer une qualité constante, même sur des séries de production importantes.
Pliage numérique et formage 3D des métaux
Le pliage numérique et le formage 3D des métaux ont ouvert de nouvelles perspectives en termes de design et de fonctionnalité des pièces chaudronnées. Les presses plieuses numériques, contrôlées par des systèmes informatiques avancés, permettent de réaliser des pliages complexes avec une précision millimétrique. Cette technologie autorise la création de formes auparavant difficiles, voire impossibles à obtenir, élargissant ainsi les possibilités de conception.
Le formage 3D, quant à lui, utilise des techniques innovantes comme l'hydroformage ou le formage incrémental. Ces procédés permettent de créer des formes tridimensionnelles complexes à partir de feuilles de métal planes, sans nécessiter d'outillages coûteux. Cette flexibilité est particulièrement avantageuse pour la production de petites séries ou de prototypes, réduisant considérablement les coûts et les délais de développement.
Techniques d'assemblage par collage structural
Les techniques d'assemblage par collage structural représentent une alternative innovante aux méthodes traditionnelles de soudage ou de rivetage. Cette approche utilise des adhésifs haute performance pour joindre les pièces métalliques, offrant plusieurs avantages significatifs. Le collage structural permet d'assembler des matériaux dissimilaires, comme des métaux et des composites, ce qui était auparavant difficile voire impossible avec les méthodes conventionnelles.
Cette technique présente également l'avantage de réduire les contraintes mécaniques au niveau des jonctions, améliorant ainsi la résistance à la fatigue des assemblages. De plus, le collage structural permet d'obtenir des structures plus légères, un atout majeur dans des secteurs comme l'aéronautique ou l'automobile où la réduction du poids est cruciale. Enfin, cette méthode offre une finition esthétique supérieure, sans les marques visibles laissées par les soudures ou les rivets.
L'adoption de ces procédés avancés de fabrication en chaudronnerie moderne permet non seulement d'améliorer la qualité et la précision des pièces produites, mais aussi d'ouvrir de nouvelles possibilités en termes de design et de fonctionnalité. Ces innovations sont essentielles pour les entreprises souhaitant rester compétitives dans un marché en constante évolution.
Matériaux innovants en chaudronnerie industrielle
L'évolution des matériaux utilisés en chaudronnerie industrielle a considérablement élargi les possibilités de conception et de fabrication. Ces nouveaux matériaux offrent des propriétés mécaniques améliorées, une résistance accrue à la corrosion et des caractéristiques spécifiques adaptées à des applications de plus en plus exigeantes.
Alliages d'aluminium haute résistance série 7000
Les alliages d'aluminium de la série 7000, notamment le 7075 et le 7050, ont révolutionné la chaudronnerie légère. Ces matériaux offrent un rapport résistance/poids exceptionnel, les rendant particulièrement attractifs pour les industries aéronautique et automobile. Leur haute résistance mécanique, combinée à une bonne résistance à la fatigue, permet de concevoir des structures légères mais robustes.
L'utilisation de ces alliages en chaudronnerie nécessite des techniques de soudage et de traitement thermique spécifiques pour préserver leurs propriétés mécaniques. Les chaudronniers modernes doivent maîtriser ces procédés pour tirer pleinement parti de ces matériaux avancés. L'adoption de ces alliages permet de réduire significativement le poids des structures tout en maintenant, voire en améliorant, leurs performances mécaniques.
Aciers inoxydables super austénitiques
Les aciers inoxydables super austénitiques représentent une avancée majeure pour les applications nécessitant une résistance exceptionnelle à la corrosion. Ces alliages, tels que le 254 SMO ou le 654 SMO, offrent une résistance inégalée aux environnements corrosifs, y compris en présence d'acides concentrés ou d'eau de mer. Leur utilisation en chaudronnerie permet de prolonger considérablement la durée de vie des équipements exposés à des conditions extrêmes.
Ces aciers présentent également une excellente résistance mécanique à haute température, les rendant idéaux pour des applications dans l'industrie chimique ou pétrochimique. Leur mise en œuvre requiert des compétences spécifiques en matière de soudage et de formage, mais offre des avantages considérables en termes de durabilité et de réduction des coûts de maintenance à long terme.
Composites métal-matrice pour applications spéciales
Les composites métal-matrice (CMM) représentent une nouvelle frontière dans le domaine des matériaux pour la chaudronnerie industrielle. Ces matériaux innovants combinent les propriétés des métaux avec celles des matériaux céramiques ou des fibres, offrant ainsi des caractéristiques uniques. Par exemple, un CMM à matrice d'aluminium renforcé de particules de carbure de silicium peut offrir une rigidité comparable à celle de l'acier tout en étant beaucoup plus léger.
L'utilisation des CMM en chaudronnerie ouvre de nouvelles possibilités pour la conception de pièces à haute performance. Ces matériaux peuvent être utilisés pour créer des composants résistants à l'usure, à la fatigue thermique, ou nécessitant une stabilité dimensionnelle exceptionnelle. Bien que leur mise en œuvre soit plus complexe que celle des métaux traditionnels, les avantages en termes de performance justifient souvent l'investissement dans ces technologies avancées.
L'intégration de ces matériaux innovants dans les processus de chaudronnerie industrielle permet de repousser les limites de la conception et de la performance des produits. Les entreprises qui maîtrisent l'utilisation de ces nouveaux matériaux peuvent se démarquer sur des marchés de niche à haute valeur ajoutée.
Logiciels de conception et simulation pour l'optimisation
L'utilisation de logiciels avancés de conception et de simulation est devenue incontournable dans la chaudronnerie industrielle moderne. Ces outils permettent non seulement d'accélérer le processus de développement, mais aussi d'optimiser les designs pour une performance maximale et une utilisation efficace des matériaux.
Modélisation 3D avancée
CATIA V6, développé par Dassault Systèmes, est l'un des logiciels de modélisation 3D les plus puissants utilisés dans l'industrie. Son utilisation en chaudronnerie permet de créer des modèles tridimensionnels complexes avec une précision exceptionnelle. Les fonctionnalités avancées de CATIA V6, telles que la conception paramétrique et associative, permettent aux ingénieurs de modifier rapidement leurs designs et d'explorer différentes variantes sans avoir à tout recommencer depuis le début.
Ce logiciel offre également des outils spécifiques pour la chaudronnerie, comme la création de développés de tôle ou la simulation de pliage. Ces fonctionnalités permettent d'anticiper les problèmes potentiels de fabrication dès la phase de conception, réduisant ainsi les coûts et les délais de production. De plus, l'intégration de CATIA V6 avec d'autres logiciels de simulation et de gestion du cycle de vie des produits (PLM) facilite la collaboration entre les différents départements impliqués dans le développement des produits.
Analyse par éléments finis
ANSYS Mechanical est un outil puissant d'analyse par éléments finis (FEA) largement utilisé en chaudronnerie industrielle. Ce logiciel permet de simuler le comportement mécanique, thermique et dynamique des structures sous différentes conditions de charge. En utilisant ANSYS, les ingénieurs peuvent prédire avec précision les contraintes, les déformations et les modes de défaillance potentiels des pièces chaudronnées.
L'un des avantages majeurs d'ANSYS est sa capacité à effectuer des analyses multiphysiques. Par exemple, il est possible de simuler simultanément les effets thermiques et mécaniques sur une structure, ce qui est particulièrement utile pour les applications impliquant des variations de température importantes. Cette approche permet d'optimiser les designs pour une meilleure résistance et durabilité, tout en minimisant le poids et la consommation de matériaux.
Optimisation topologique pour l'allègement des structures
L'optimisation topologique est une technique avancée qui révolutionne la conception en chaudronnerie. Cette approche utilise des algorithmes sophistiqués pour déterminer la distribution optimale du matériau dans une pièce, en fonction des contraintes mécaniques et des objectifs de performance. Le résultat est souvent une structure organique, légère mais extrêmement résistante.
Des logiciels comme Altair OptiStruct ou ANSYS Topology Optimization permettent de réaliser ce type d'optimisation. L'utilisation de ces outils en chaudronnerie peut conduire à des réductions de poids significatives, parfois jusqu'à 50%, tout en maintenant ou même en améliorant les performances mécaniques. Cette approche est particulièrement précieuse dans les industries où le poids est un facteur critique, comme l'aérospatiale ou l'automobile.
L'optimisation topologique ouvre également de nouvelles possibilités en termes de design. Les formes complexes générées par ces algorithmes, souvent difficiles à réaliser avec les méthodes de fabrication traditionnelles, deviennent accessibles grâce aux techniques de fabrication additive métallique. Cette synergie entre optimisation topologique et impression 3D métal représente une
frontière entre optimisation topologique et impression 3D métal représente une avancée majeure dans la conception de pièces chaudronnées complexes et légères.
L'utilisation de ces logiciels avancés de conception et de simulation permet aux entreprises de chaudronnerie d'optimiser leurs produits, de réduire les coûts de développement et de fabrication, et d'accélérer la mise sur le marché de solutions innovantes. La maîtrise de ces outils est devenue un avantage concurrentiel majeur dans l'industrie.
Gestion de production lean en chaudronnerie moderne
L'adoption des principes du lean manufacturing dans la chaudronnerie moderne a permis d'optimiser considérablement les processus de production. Cette approche, centrée sur l'élimination des gaspillages et l'amélioration continue, a transformé la façon dont les ateliers de chaudronnerie opèrent au quotidien.
L'un des piliers de la gestion lean en chaudronnerie est la mise en place de flux tirés. Cette méthode consiste à produire uniquement en fonction de la demande réelle du client, évitant ainsi la surproduction et réduisant les stocks. Pour y parvenir, de nombreuses entreprises ont adopté des systèmes kanban, qui permettent une gestion visuelle des flux de production et d'approvisionnement.
La réduction des temps de changement de série (SMED - Single Minute Exchange of Die) est une autre technique lean largement appliquée dans la chaudronnerie moderne. En optimisant les procédures de réglage des machines, les entreprises peuvent réduire considérablement les temps d'arrêt entre deux productions différentes, augmentant ainsi la flexibilité et la réactivité de l'atelier.
L'amélioration continue, ou Kaizen, est au cœur de la démarche lean. Dans les ateliers de chaudronnerie, cela se traduit par la mise en place de groupes de résolution de problèmes et l'encouragement des suggestions d'amélioration venant des opérateurs. Cette approche permet non seulement d'optimiser les processus, mais aussi de valoriser l'expertise des employés et d'améliorer leur engagement.
La gestion visuelle joue également un rôle crucial dans la chaudronnerie lean. L'utilisation de tableaux de bord, d'indicateurs de performance (KPI) affichés dans l'atelier, et de systèmes d'andon pour signaler rapidement les problèmes, permet une meilleure communication et une réactivité accrue face aux aléas de production.
L'implémentation des principes lean dans la chaudronnerie moderne ne se limite pas à l'optimisation des processus de fabrication. Elle implique un changement culturel profond, favorisant la responsabilisation des employés, la résolution collaborative des problèmes et une focalisation constante sur la création de valeur pour le client.
Normes et certifications pour la chaudronnerie de pointe
Dans un secteur aussi exigeant que la chaudronnerie industrielle, le respect des normes et l'obtention de certifications sont essentiels pour garantir la qualité, la sécurité et la conformité des produits. Ces standards jouent un rôle crucial dans la compétitivité des entreprises sur le marché international.
La norme ISO 9001 est fondamentale pour les entreprises de chaudronnerie. Elle définit les exigences pour un système de management de la qualité, assurant que les processus sont bien documentés et contrôlés. Pour les chaudronniers travaillant dans des secteurs spécifiques, des certifications complémentaires sont souvent nécessaires. Par exemple, la norme EN 1090 est incontournable pour la fabrication de structures en acier et en aluminium dans le secteur de la construction.
Pour les applications dans l'industrie nucléaire, la certification RCC-M (Règles de Conception et de Construction des Matériels Mécaniques des îlots nucléaires REP) est essentielle. Elle garantit que les équipements sous pression respectent les exigences strictes de sûreté nucléaire. De même, la norme ASME (American Society of Mechanical Engineers) est cruciale pour les chaudronniers travaillant sur des projets internationaux, notamment dans le secteur pétrolier et gazier.
La certification ISO 3834 est spécifique au soudage et devient de plus en plus importante dans la chaudronnerie moderne. Elle définit les exigences de qualité pour le soudage par fusion des matériaux métalliques, couvrant tous les aspects du processus, de la conception à la fabrication.
En matière de sécurité et de santé au travail, la norme ISO 45001 est en train de devenir la référence. Elle aide les entreprises à réduire les risques professionnels et à améliorer les conditions de travail, un aspect particulièrement important dans les ateliers de chaudronnerie où les risques liés à la manipulation de matériaux lourds et aux procédés de soudage sont omniprésents.
L'adhésion à ces normes et l'obtention de ces certifications ne sont pas seulement des exigences réglementaires, mais représentent aussi un véritable avantage concurrentiel. Elles démontrent l'engagement de l'entreprise envers la qualité, la sécurité et l'excellence opérationnelle, rassurrant ainsi les clients et ouvrant la porte à de nouveaux marchés.
L'optimisation de la production grâce à la chaudronnerie industrielle moderne repose sur une combinaison de technologies avancées, de matériaux innovants, de logiciels performants, de techniques de gestion lean et de respect des normes les plus strictes. Les entreprises qui réussissent à intégrer ces différents aspects sont celles qui se démarquent sur un marché de plus en plus compétitif et exigeant. L'avenir de la chaudronnerie industrielle s'annonce passionnant, avec des innovations continues qui promettent de repousser encore les limites de ce que l'on peut réaliser avec le métal.