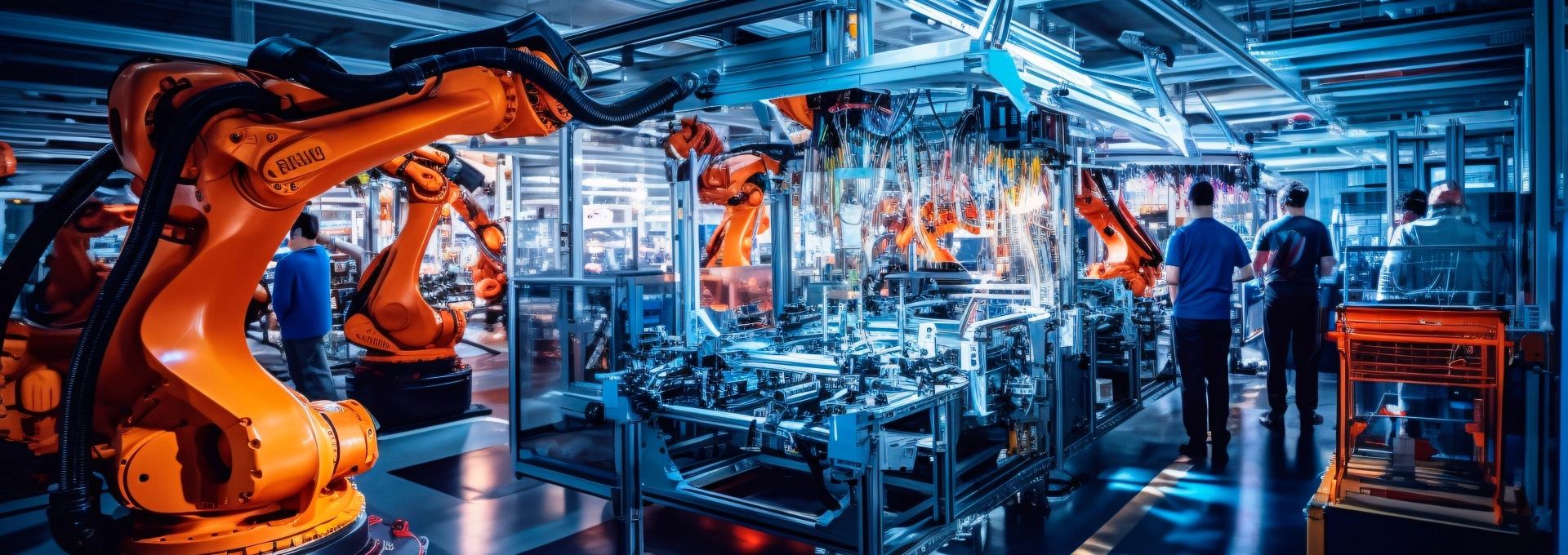
L'adaptation des lignes de production existantes aux technologies 4.0 est un processus complexe mais essentiel pour rester compétitif dans l'industrie moderne. Une approche méthodique, combinant une évaluation rigoureuse des systèmes actuels, une intégration progressive des nouvelles technologies, et une mesure continue des performances, est la clé du succès. En surmontant les défis techniques et en formant adéquatement le personnel, les entreprises peuvent non seulement améliorer leur efficacité opérationnelle, mais aussi se positionner comme des leaders dans l'ère de l'industrie numérique. La transformation vers l'industrie 4.0 n'est pas seulement une question de technologie, mais une opportunité de repenser fondamentalement les processus de production pour créer une valeur durable à long terme.
Évaluation des systèmes de production actuels pour l'intégration 4.0
Avant d'entamer toute modernisation, une évaluation approfondie des systèmes de production existants s'impose. Cette étape initiale permet d'identifier les points forts et les faiblesses des installations actuelles, ainsi que leur potentiel d'intégration des technologies liées à la révolution industrielle 4.0. L'analyse doit prendre en compte plusieurs aspects clés, notamment l'état des équipements, les processus de fabrication, les systèmes de contrôle et la connectivité des machines.
Une approche systématique d'évaluation implique généralement la collecte de données sur la performance actuelle des lignes de production. Ces informations servent de référence pour mesurer l'impact des futures améliorations. Les indicateurs à considérer incluent la productivité, la qualité, la flexibilité et la consommation énergétique. Une cartographie détaillée des flux de production et d'information aide à visualiser les opportunités d'optimisation.
L'évaluation doit également tenir compte de la compatibilité des systèmes existants avec les nouvelles technologies. Certains équipements plus anciens peuvent nécessiter des mises à niveau ou des remplacements pour s'intégrer dans un environnement 4.0. Il est crucial d'identifier les goulots d'étranglement potentiels qui pourraient entraver la mise en œuvre des nouvelles technologies.
Une fois l'évaluation terminée, les entreprises peuvent classer leurs actifs en fonction de leur potentiel d'amélioration et de leur importance stratégique. Cette hiérarchisation guide les décisions d'investissement et permet de concentrer les efforts sur les domaines offrant le meilleur retour sur investissement.
Technologies clés pour la modernisation des lignes de production
La transformation des lignes de production existantes en systèmes 4.0 repose sur l'intégration de plusieurs technologies clés. Le cœur de cette transformation réside dans l'adoption des principes de la révolution industrielle 4.0. Ces innovations permettent de créer un environnement de fabrication intelligent, connecté et hautement adaptatif. Voici un aperçu des principales technologies à considérer pour moderniser les installations existantes :
Capteurs IoT et systèmes de collecte de données en temps réel
L'industrie numérique repose sur la capacité à collecter et analyser des données en temps réel. Les capteurs IoT (Internet des Objets) jouent un rôle crucial dans cette transformation. Ils peuvent être installés sur les équipements existants pour surveiller divers paramètres tels que la température, la vibration, la pression ou la consommation d'énergie. Ces capteurs fournissent un flux continu de données qui alimentent les systèmes d'analyse et de contrôle.
L'intégration de capteurs IoT dans les lignes de production existantes permet de créer un jumeau numérique de l'usine. Ce modèle virtuel offre une visibilité en temps réel sur l'ensemble des opérations, facilitant ainsi la prise de décision et l'optimisation des processus. Par exemple, des capteurs de vibration installés sur des machines critiques peuvent détecter des anomalies avant qu'elles ne conduisent à des pannes coûteuses.
La mise en place d'un réseau de capteurs nécessite une infrastructure de communication robuste. Les technologies sans fil comme le Wi-Fi industriel, le Bluetooth Low Energy (BLE) ou les réseaux cellulaires 5G offrent la flexibilité nécessaire pour connecter un grand nombre de dispositifs sans perturber les opérations existantes.
Plateformes d'analyse prédictive pour l'optimisation des processus
Les données collectées par les capteurs IoT prennent tout leur sens lorsqu'elles sont analysées par des plateformes d'intelligence artificielle (IA) et d'apprentissage automatique. Ces outils permettent de passer d'une maintenance réactive à une maintenance prédictive, réduisant ainsi les temps d'arrêt imprévus et optimisant l'utilisation des équipements.
Les plateformes d'analyse prédictive utilisent des algorithmes avancés pour identifier des modèles dans les données opérationnelles et prédire les problèmes potentiels avant qu'ils ne surviennent. Par exemple, en analysant les données historiques et en temps réel d'une ligne d'assemblage, le système peut prédire quand une pièce spécifique risque de tomber en panne et planifier la maintenance en conséquence.
L'intégration de ces plateformes dans les systèmes existants nécessite souvent la mise en place d'une architecture de données cohérente. Cela peut impliquer la création d'un data lake centralisé ou l'utilisation de solutions edge computing pour traiter les données au plus près de leur source. La sécurité des données est également un aspect crucial à prendre en compte lors de la mise en œuvre de ces systèmes.
Solutions de robotique collaborative et d'automatisation avancée
L'introduction de robots collaboratifs, ou cobots
, représente une évolution majeure dans l'adaptation des lignes de production existantes. Contrairement aux robots industriels traditionnels, les cobots sont conçus pour travailler en étroite collaboration avec les opérateurs humains, combinant la flexibilité humaine avec la précision et l'endurance des machines.
Les cobots peuvent être intégrés progressivement dans les lignes de production existantes, sans nécessiter de refonte complète des processus. Ils excellent dans les tâches répétitives ou ergonomiquement difficiles, libérant ainsi les travailleurs pour des activités à plus forte valeur ajoutée. Par exemple, un cobot peut être utilisé pour le chargement et le déchargement de pièces dans une machine-outil, améliorant la productivité tout en réduisant les risques de blessures pour les opérateurs.
L'automatisation avancée va au-delà de la simple robotisation. Elle inclut des systèmes de vision artificielle pour le contrôle qualité, des véhicules à guidage automatique (AGV) pour la logistique interne, et des systèmes de fabrication additive pour la production de pièces complexes ou personnalisées. Ces technologies, intrinsèquement liées à la révolution industrielle 4.0, peuvent être progressivement intégrées dans les lignes existantes pour augmenter la flexibilité et la capacité de production.
Stratégies d'implémentation progressive des technologies 4.0
La transition vers l'industrie 4.0 ne se fait pas du jour au lendemain. Une approche progressive et bien planifiée est essentielle pour minimiser les perturbations et maximiser les bénéfices. Voici les étapes clés pour une implémentation réussie de l'alignement des technologies 4.0 dans les lignes de production existantes :
Cartographie des processus et identification des points d'amélioration
La première étape consiste à réaliser une cartographie détaillée des processus de production actuels. Cette analyse permet d'identifier les goulots d'étranglement, les inefficacités et les opportunités d'amélioration. Utilisez des outils de modélisation des processus pour créer une représentation visuelle de vos flux de production et d'information.
Impliquez les opérateurs et les superviseurs de ligne dans ce processus. Leur expérience pratique est inestimable pour identifier les points critiques où l'introduction de technologies 4.0 pourrait avoir le plus grand impact. Par exemple, vous pourriez découvrir qu'un simple ajout de capteurs sur une machine clé pourrait considérablement réduire les temps d'arrêt non planifiés.
Une fois les points d'amélioration identifiés, priorisez-les en fonction de leur impact potentiel et de la facilité de mise en œuvre. Concentrez-vous d'abord sur les quick wins qui peuvent démontrer rapidement la valeur de la transformation numérique dans le cadre de la révolution industrielle 4.0.
Planification des phases d'intégration et gestion du changement
Élaborez un plan d'intégration par phases qui s'aligne sur vos objectifs stratégiques et vos contraintes opérationnelles. Commencez par des projets pilotes sur des zones limitées de votre production pour tester et affiner votre approche. Ces projets pilotes servent de preuve de concept et aident à gagner l'adhésion de toutes les parties prenantes.
La gestion du changement est cruciale pour le succès de votre transformation. Communiquez clairement les objectifs et les bénéfices attendus à tous les niveaux de l'organisation. Formez des champions du changement parmi vos employés pour promouvoir l'adoption des nouvelles technologies et pratiques.
Prévoyez des périodes de transition où les anciens et les nouveaux systèmes fonctionneront en parallèle. Cela permet de minimiser les risques et d'assurer une continuité opérationnelle. Établissez des points de contrôle réguliers pour évaluer les progrès et ajuster votre stratégie si nécessaire.
Formation du personnel aux nouvelles technologies et compétences
La transformation numérique nécessite une évolution des compétences de votre main-d'œuvre. Développez un programme de formation complet qui couvre non seulement les aspects techniques des nouvelles technologies, mais aussi les nouvelles méthodes de travail qu'elles impliquent.
Utilisez une variété de méthodes de formation, y compris des sessions en présentiel, des modules d'e-learning et des simulations pratiques. La réalité virtuelle et augmentée peut être particulièrement efficace pour former les opérateurs aux nouvelles procédures sans interrompre la production.
Encouragez une culture d'apprentissage continu au sein de votre organisation. Les technologies 4.0 évoluent rapidement, et votre personnel doit être capable de s'adapter à ces changements. Considérez la création de centres d'excellence internes pour partager les meilleures pratiques et favoriser l'innovation dans le contexte de la révolution industrielle 4.0.
Défis techniques de l'adaptation des équipements existants
L'intégration des technologies 4.0 dans les lignes de production existantes présente plusieurs défis techniques qu'il convient d'anticiper et de surmonter. L'un des principaux obstacles est la compatibilité entre les systèmes anciens et les nouvelles technologies. De nombreuses usines utilisent encore des équipements qui n'ont pas été conçus pour être connectés ou pour communiquer avec d'autres systèmes.
Pour résoudre ce problème, plusieurs approches peuvent être envisagées. L'utilisation de passerelles IoT
permet de connecter des machines plus anciennes au réseau de l'usine. Ces passerelles agissent comme des traducteurs, convertissant les signaux des équipements existants en données compatibles avec les protocoles modernes de communication industrielle, un élément clé de la révolution industrielle 4.0.
Un autre défi majeur est la gestion de la cybersécurité. En connectant les systèmes de production à Internet, vous augmentez potentiellement la surface d'attaque pour les cybercriminels. Il est crucial de mettre en place une stratégie de sécurité robuste qui inclut la segmentation du réseau, l'authentification multifactorielle et des mises à jour régulières des logiciels et des firmwares.
La gestion des données représente également un défi technique important. Les capteurs IoT génèrent un volume considérable de données qui doivent être stockées, traitées et analysées efficacement. La mise en place d'une infrastructure de données adaptée, capable de gérer ces flux massifs d'informations, est essentielle. Cela peut nécessiter l'investissement dans des solutions de edge computing pour traiter les données au plus près de leur source, réduisant ainsi la latence et la charge sur le réseau. Ce défi est particulièrement pertinent dans le contexte de la révolution industrielle 4.0.
Mesure de performance et ROI des adaptations 4.0
L'évaluation du retour sur investissement (ROI) des adaptations 4.0 est cruciale pour justifier les investissements et guider les futures décisions. La mesure de performance doit être holistique, prenant en compte non seulement les gains financiers directs, mais aussi les améliorations qualitatives et l'impact sur la compétitivité à long terme de l'entreprise. L'implémentation réussie des technologies de la révolution industrielle 4.0 dépend fortement de cette évaluation précise.
Indicateurs clés de performance pour l'évaluation de la transformation
Pour évaluer efficacement l'impact des adaptations 4.0, il est nécessaire de définir un ensemble d'indicateurs clés de performance (KPI) pertinents. Ces KPI doivent couvrir différents aspects de la performance opérationnelle, tels que :
- Productivité (ex : taux de production, temps de cycle)
- Qualité (ex : taux de défauts, coûts de non-qualité)
- Flexibilité (ex : temps de changement de série, variété des produits)
- Efficacité énergétique (ex : consommation d'énergie par unité produite)
- Utilisation des actifs (ex : taux de disponibilité des équipements, OEE)
Il est important de choisir des indicateurs qui sont directement influencés par les technologies 4.0 mises en place. Par exemple, si vous avez implémenté un système de maintenance prédictive, vous devriez suivre la réduction des temps d'arrêt non planifiés et l'augmentation de la durée de vie des équipements. Ces données sont essentielles pour évaluer le succès de votre intégration de la révolution industrielle 4.0.
Analyse comparative pré et post-adaptation des lignes de production
Pour évaluer précisément l'impact des adaptations 4.0, il est essentiel de réaliser une analyse comparative approfondie entre la situation avant et après la transformation. Cette comparaison doit s'appuyer sur des données concrètes collectées sur une période suffisamment longue pour être significative.
Commencez par établir une base de référence solide avant le début des adaptations. Documentez soigneusement les performances de vos lignes de production sur tous les KPI identifiés précédemment. Cette étape peut nécessiter la mise en place de systèmes de collecte de données supplémentaires si les informations actuelles sont insuffisantes.
Après la mise en œuvre des technologies 4.0, surveillez attentivement les mêmes indicateurs sur une période comparable. Assurez-vous de prendre en compte les éventuelles variations saisonnières ou autres facteurs externes qui pourraient influencer les résultats. L'utilisation d'outils statistiques avancés peut vous aider à isoler l'impact réel des adaptations 4.0 des autres variables.
Calcul du retour sur investissement à court et long terme
Le calcul du retour sur investissement (ROI) à court et à long terme est essentiel pour évaluer la rentabilité de tout projet ou investissement. À court terme, le ROI est souvent mesuré en comparant les gains financiers immédiats obtenus à partir de l'investissement initial avec les coûts engagés. Cette approche permet de déterminer rapidement l'efficacité d'un investissement et d'ajuster les stratégies si nécessaire.
À long terme, le calcul du ROI prend en compte des variables supplémentaires telles que la dépréciation, les coûts d'entretien, et les bénéfices continus générés sur une période prolongée. Il est crucial d'inclure ces facteurs pour obtenir une vision complète de la viabilité financière de l'investissement lié à la révolution industrielle 4.0.
En intégrant à la fois les perspectives à court et à long terme, les entreprises et les investisseurs peuvent prendre des décisions plus éclairées, maximiser leurs gains et minimiser les risques associés à leurs investissements.